6 Must-Have Features of a Warehouse Management System (WMS)
Blogs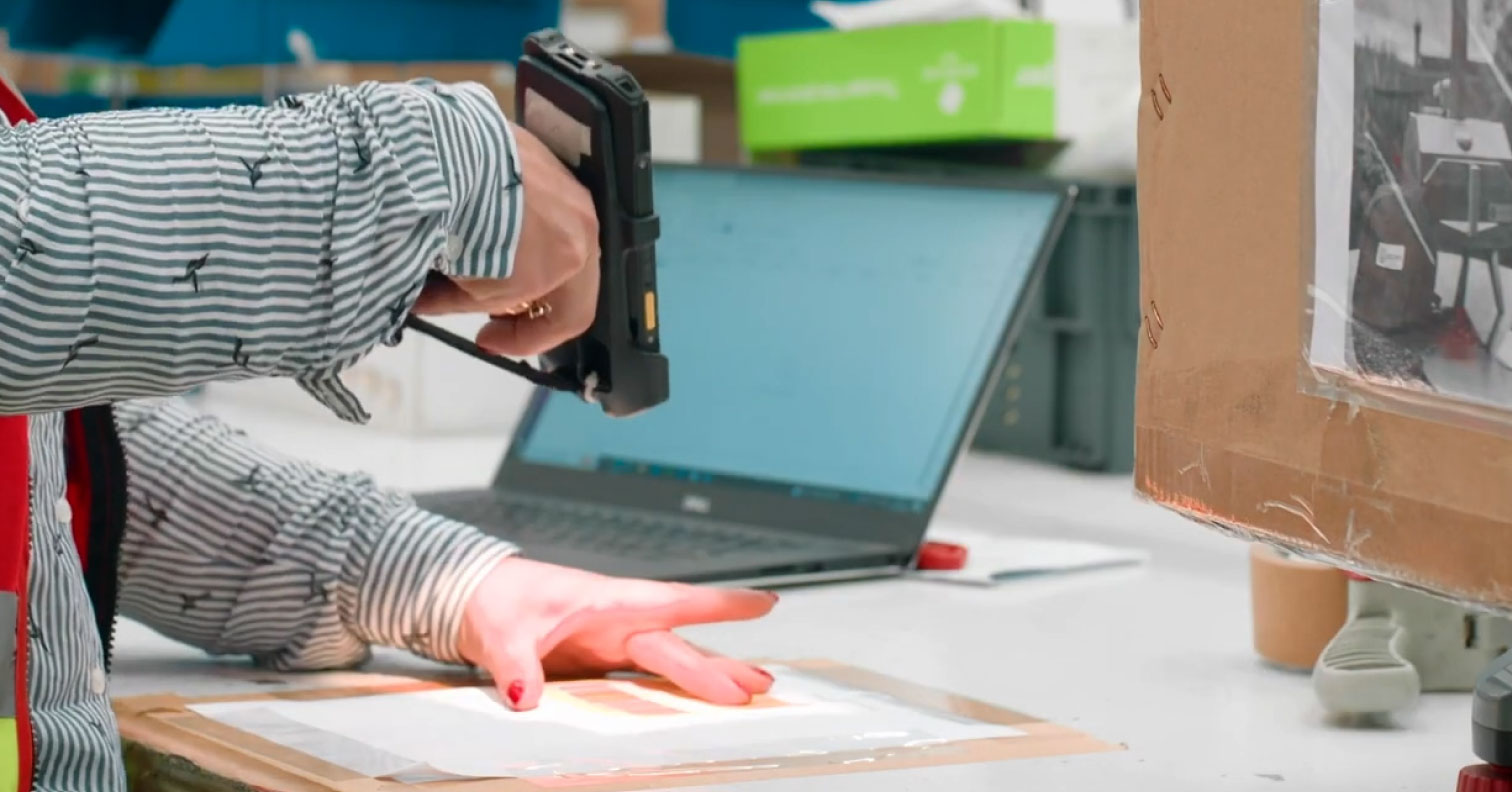
Are you wondering if it’s time to consider a Warehouse Management System (WMS) to enhance your logistics capabilities? Given the competitive warehousing landscape, efficient, real-time warehouse management is no longer a luxury but a necessity. In fact, with WMS adoption surging — forecasted to grow 15.4% annually until 2033 [1] — it’s evident that businesses are embracing these systems to stay ahead of the curve.
So, if your warehouse is plagued by inventory inaccuracies, sluggish operations, or mounting pressure from a fast-changing supply chain, you need a WMS. That said, not all WMS solutions are created equal. You need to ensure it comprises of the key features that solve challenges and support your business goals. This will guarantee streamlined inventory management, enhanced order fulfillment, and ultimately a big boost your bottom line.
In this article, we will explore the must-have features of a warehouse management system that will take your business to the next level. From real-time inventory tracking and barcode scanning to automated reporting and integration capabilities, the following WMS features will help you stay on top of your inventory and ensure smooth operations:
- Inventory Management
- Order Fulfillment and Tracking
- Integration with Other Systems and Technologies
- Reporting and Analytics
- Scalability and Flexibility of the System
- User-Friendly Interface and Ease of Use
Inventory Management
A robust Warehouse Management System (WMS) should offer advanced inventory management capabilities to help optimize stock levels, reduce carrying costs, and improve overall efficiency. Real-time inventory tracking is a crucial feature that allows businesses to monitor retail and e-commerce stock levels, locations, and movements in real time, providing accurate and up-to-date information on inventory quantities.
Beyond real-time tracking, a WMS will also offer features like cycle counting, warehouse space optimization, and automated replenishment to help maintain accurate inventory records and prevent stockouts or overstocking. When these WMS features are automated, they reduce manual errors, improve inventory accuracy, and ensure that the right amount of stock is always available on hand. Additionally, these capabilities will help in identifying slow-moving or obsolete stock, enabling you to make informed decisions about pricing, promotions, and stock liquidation.
Furthermore, a WMS with inventory management capabilities should provide in-depth reporting and analytics tools to gain insights into inventory performance. By analyzing key metrics such as stock turnover rates, carrying costs, and order fulfillment times, you can identify areas for improvement, optimize inventory levels, and make data-driven decisions to enhance overall warehouse operations.
Order Fulfillment and Tracking
Efficient order fulfillment is essential for meeting customer expectations and ensuring timely deliveries. A Warehouse Management System (WMS) with robust order fulfillment and tracking functionality will streamline the picking, packing, and shipping, leading to faster order processing and improved customer satisfaction.
It is also beneficial to have a WMS with features that will optimize picking routes and automate picking processes. A warehouse management system with these capabilities will intelligently group orders, optimize pick paths, and assign tasks to warehouse staff based on availability. This in turn, will reduce travel time, improve picking accuracy, and increase overall efficiency. Automated packing processes can further enhance order fulfillment by reducing errors, standardizing packing procedures, and ensuring that orders are packed securely.
Real-time tracking is another critical feature that will improve the order fulfillment processes. By providing visibility into order status, shipment tracking, and delivery time, you keep customers informed about their orders and proactively address any issues that may arise. This transparency not only enhances the customer experience but also helps identify potential bottlenecks in the fulfillment process. That way, necessary adjustments are made to improve efficiency.
Discover the Advantages of Robust Order Fulfillment and TrackingIntegration with Other Systems and Technologies
A WMS that can seamlessly integrate with other systems and technologies, such as Enterprise Resource Planning (ERP) systems, e-commerce platforms, shipping carriers, etc., will help you streamline your operations, reduce manual data entry, and improve data accuracy.
Integration with ERP systems allows the synchronization of data between a WMS and other business applications, ensuring that inventory levels, purchase information, and client data are consistent and tracked in a timely manner. This kind of integration not only eliminates the need for manual data entry but also enables businesses to make more informed decisions by leveraging real-time, accurate data.
Similarly, integrating a WMS with e-commerce platforms will help you automate order processing, update inventory levels in real-time, and provide customers with accurate order status information. By connecting your WMS with e-commerce platforms, you improve order fulfillment accuracy, reduce order processing time, and enhance the overall customer experience. Additionally, integration with shipping carriers will streamline the shipping process, generate shipping labels automatically, and track shipments in real-time, leading to faster and more efficient deliveries.
Reporting and Analytics
Data-driven decision-making is essential for optimizing warehouse operations and improving overall efficiency. A Warehouse Management System (WMS) that offers insightful reporting and analytics capabilities will help you gain valuable information into your operations, identify areas for improvement, and enable informed decision making.
The reporting capabilities of a WMS allow you to generate detailed reports on key metrics such as inventory levels, order fulfillment time, picking accuracy, and warehouse productivity. By analyzing these reports, you can identify trends, spot inefficiencies, and make data-driven decisions to optimize warehouse operations. Additionally, customizable reporting options enable you to tailor reports to your specific needs and track performance against specific KPIs.
Advanced analytics tools within a WMS will provide you with deeper insights into your operations by analyzing historical data, predicting future trends, and identifying opportunities for improvement. By leveraging predictive analytics, you can forecast demand, optimize inventory levels, and streamline order fulfillment processes (especially during sales periods). Moreover, predictive analytics can help you make proactive decisions by recommending actions to improve efficiency, reduce costs, and enhance overall warehouse performance.
Scalability and Flexibility of the System
As a 3PL, brand, distributor, or retailer, your business will grow and evolve, which means your warehouse management needs will change. So, your Warehouse Management System must be able to adapt to your changing requirements. Scalability and flexibility are essential WMS features to consider, as they ensure that the system will grow with your business and accommodate new functionalities, users, and warehouse or store locations as needed.
A scalable WMS allows you to leverage new features, upgrade software, and optimize storage capacity without disrupting existing operations. It also enables you to adapt to changing market conditions, expand product offerings, and meet the evolving needs of customers.
Flexibility is another critical aspect to consider when choosing a WMS. A flexible system allows you to customize workflows, adjust settings, and integrate new technologies to meet specific warehouse management needs. By providing configurable options and adaptable features, a flexible WMS empowers you to optimize your operations, improve efficiency, and stay ahead of the competition in a rapidly changing business landscape.
User-Friendly Interface and Ease of Use
A user-friendly interface and intuitive design are crucial to ensure your warehouse staff quickly learns to navigate your Warehouse Management System. A system with a clean, intuitive interface reduces training time, minimizes errors, and improves overall efficiency by making it easy for users to access key features and perform tasks efficiently.
An easy-to-use WMS must offer features such as customizable dashboards, drag-and-drop functionality, and clear navigation menus to help users find information quickly and perform tasks with minimal effort. By simplifying complex processes and presenting information in a clear and concise manner, a user-friendly interface enhances productivity, reduces user errors, and improves employee satisfaction.
A WMS with built-in help guides, tutorials, and tips further enhances the user experience by providing the support needed to navigate the system effectively and troubleshoot common issues without waiting. Securing ongoing training and support will ensure that your warehouse staff are proficient in using the WMS, leading to increased adoption rates, improved efficiency, and ultimately, a more productive and successful warehouse.
Experience the Must-Have Features of a WMSConclusion: Choosing the Right Warehouse Management System for Your Business
Selecting the right Warehouse Management System (WMS) is a critical decision when looking to optimize warehouse operations and improve overall efficiency. By considering key WMS features such as inventory management, order fulfillment, integration, reporting and analytics, scalability, flexibility, and user-friendliness, you can choose a WMS that meets your specific needs and helps achieve your warehouse management goals.
A well-designed WMS will streamline inventory management, enhance order fulfillment, improve data accuracy, and provide you with valuable insights into your operations. So, whether you operate a small warehouse or a large distribution center, the right WMS will revolutionize your operations, increase efficiency, and boost your bottom line. By investing in a powerful WMS with the essential features outlined in this article, you will take your warehouse management to the next level and stay ahead of the competition in today’s fast-paced business environment.
FAQs
1. How does real-time inventory tracking benefit warehouse operators?
Real-time inventory tracking allows you to monitor stock levels, movements, and locations instantly, reducing errors, preventing stockouts or overstocking, and ensuring accurate inventory records.
2. How does a WMS improve the order fulfillment processes?
A WMS can optimize picking routes, automate packing, and provide real-time order tracking, leading to faster order processing, fewer errors, and improved customer satisfaction.
3. How does a WMS integrate with other business systems?
A WMS can integrate via open APIs with ERP systems, e-commerce platforms, and shipping carriers, ensuring seamless data flow, reducing manual data entry, and improving overall operational efficiency.
References –