What is a Fulfillment Center & How does It Work?
Blogs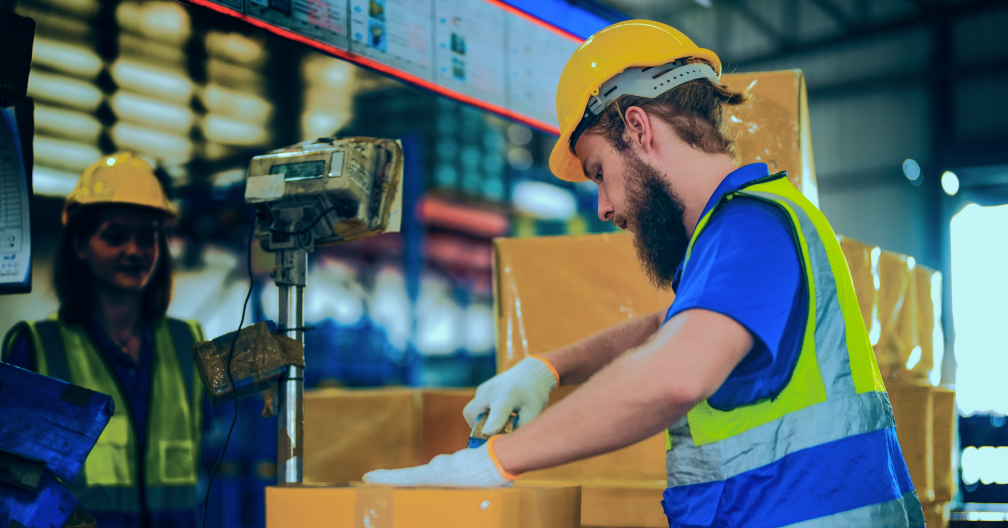
The ecommerce boom has fundamentally changed what the market expects from shipping and delivery–Two-day, next-day, and even same-day delivery. This heightened expectation is compounded by the pressure to reduce operational costs while managing increasingly complex multi-channel fulfillment requirements.
This is where fulfillment centers enter the picture—as a fundamentally different operational model designed to address these growing pains. In this blog, we will break down what fulfillment centers are, how they operate differently from traditional warehouses, what tangible benefits they deliver to your bottom line, and how to evaluate whether your operation needs to evolve toward this model.
What is a Fulfillment Center?
A fulfillment center is a purpose-built operation designed to efficiently receive, store, process, and ship individual customer orders. While traditional warehouses excel at bulk storage and occasional large shipments, fulfillment centers are optimized to process high-volume, small-orderswith speed and accuracy as top priorities.
Third-party fulfillment centers take this concept further by providing specialized order fulfillment services to multiple businesses, leveraging shared infrastructure, labor, technology, and carrier relationships to achieve economies of scale that would be difficult for individual companies to match.
For logistics teams, the distinction matters because fulfillment centers measure success differently. Where warehouse KPIs typically focus on storage utilization and inventory accuracy, fulfillment centers prioritize metrics like order cycle time, same-day shipping percentages, and order accuracy rates—metrics directly tied to customer satisfaction and retention.
How Fulfillment Centers Work: Step-by-Step Process
Behind every next-day or same-day delivery package is a carefully orchestrated fulfillment operation. While warehouses and fulfillment centers might look similar from the outside, their internal processes reveal key differences in how they handle products and orders. Walk through what actually happens inside a fulfillment center from the moment inventory arrives until packages leave for delivery–and why it has become fundamental to today’s booming ecommerce sector: :
- Inbound Flow: Unlike batch-focused warehouse receiving, fulfillment centers process incoming inventory with urgency, often making new stock available for orders within hours of arrival. Fast SKU verification, quality checks, and system entry are prioritized to maintain perpetual inventory accuracy.
- Storage and Inventory Management: Products are stored using demand-based slotting strategies—high-velocity items in easily accessible locations, often in forward pick areas, with slower-moving inventory in secondary locations. Real-time WMS tracking eliminates the inventory “black holes” that plague traditional warehouse operations.
- Order Processing: When orders arrive, they’re immediately prioritized based on service level commitments, carrier cutoff times, and resource availability. Orders for similar items or shipping destinations are often batched to maximize picking efficiency while maintaining promised delivery windows.
- Picking: Fulfillment centers employ zone-based, batch, or cluster picking strategies to maximize efficiency based on order profiles. Advanced operations incorporate pick-to-light, voice-guided picking, or semi-automated systems to reduce error rates while increasing throughput.
- Packing: Rather than standard box sizes, fulfillment centers select packaging based on order contents, optimizing for both protection and dimensional weight. Automated systems often suggest the optimal packaging configuration to minimize shipping costs.
- Shipping: Multi-carrier shipping stations automatically determine the most cost-effective carrier and service level to meet delivery promises. Rate-shopping across dozens of service options happens in seconds, capturing savings on every package.
- Returns Processing: Streamlined returns handling includes automated routing, inspection, disposition decision trees, and inventory reintegration workflows designed to recapture value and maintain accurate inventory levels.
These processes are orchestrated through integrated systems that eliminate the data silos common in traditional warehouse operations, providing end-to-end visibility and accountability.
Why Businesses Need a Fulfillment Center
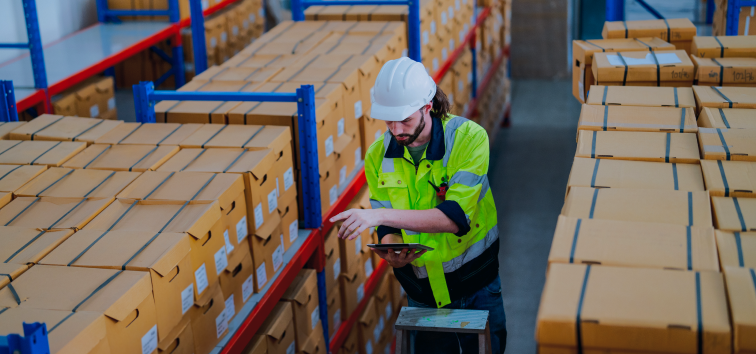
Switching to a fulfillment center model represents a significant business decision, not just a change in warehouse procedures. Before making this investment, it’s worth understanding exactly what benefits these specialized operations deliver and how they translate to better customer experiences and healthier profit margins:
Cost-Per-Order Reduction
A well-run fulfillment center typically achieves 15-30% lower cost-per-order than traditional warehouse operations handling e-commerce fulfillment. This comes through labor efficiency, optimized carrier selection, reduced error rates, and shared overhead costs when using third-party providers.
Service Level Improvements
Fulfillment centers routinely achieve same-day shipping for orders received by mid-afternoon—a service level that traditional warehouses struggle to match without excessive labor costs. This translates directly to faster delivery times and higher customer satisfaction scores.
Flexibility Without Fixed Costs
The fulfillment center model—whether in-house or outsourced—provides operational elasticity to handle seasonal peaks, promotion-driven spikes, and growth periods without the capital expenditure of warehouse expansion or the inefficiency of carrying excess capacity during slower periods.
Carrier Rate Advantages
By aggregating shipping volume (particularly in third-party arrangements) and implementing sophisticated rate-shopping technology, fulfillment centers can secure lower shipping rates often below standard commercial rates, with savings increasing as dimensional weight pricing becomes more prevalent.
Technology Leverage
Modern fulfillment centers employ advanced WMS, OMS, and TMS systems that would require significant capital and IT resources to implement independently. These systems deliver inventory accuracy, processing efficiency, and business intelligence capabilities that drive continuous improvement.
Multi-Channel Capabilities
Unlike traditional warehouses that may struggle with the complexity of serving both retail replenishment and direct-to-consumer channels, fulfillment centers are designed to handle diverse order profiles through the same infrastructure, simplifying inventory management and order routing.
Fulfillment Center vs. Warehouse: Key Differences
Warehouses and fulfillment centers might seem like different names for the same thing. However, they serve distinctly different purposes in the supply chain. Understanding these practical differences helps businesses identify improvement opportunities and determine which model best supports their growth plans:
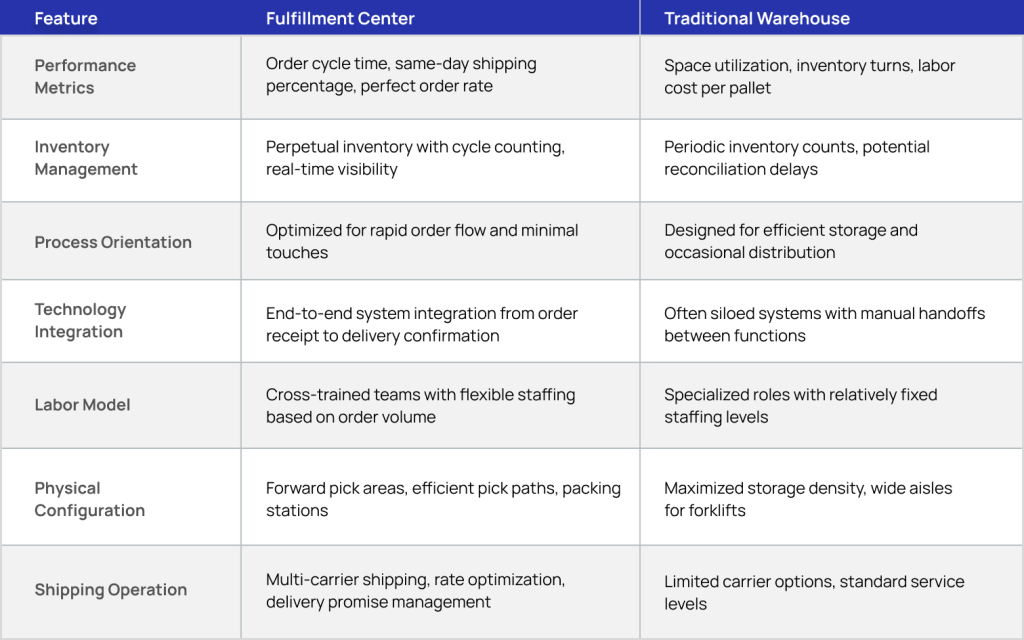
How to Choose the Right Fulfillment Center for Your Business
With so many fulfillment options available—from handling everything in-house to fully outsourced solutions—finding the right fit requires looking beyond marketing claims. A systematic approach to evaluating potential partners helps identify which solutions genuinely align with your specific business needs:
Network Optimization Analysis
Start with a data-driven analysis of order patterns by geographic region. The ideal fulfillment center locations should minimize the weighted average shipping distance to end-customers, with specific attention to high-volume shipping lanes. Each shipping zone reduction typically yields 8-15% cost savings on parcel shipments.
System Integration Capabilities
The fulfillment center’s technology infrastructure should integrate seamlessly with e-commerce platforms, ERP, and customer service systems. Look for established API connections, real-time inventory updates, and order status visibility to eliminate the manual reconciliation that erodes efficiency.
Peak Volume Management
Evaluate how the fulfillment center handles capacity planning for seasonal peaks. Request specific information about their staffing model, equipment capacity, and space allocation during high-volume periods. The best partners maintain consistent service levels regardless of volume fluctuations.
Total Cost Analysis
Rather than focusing solely on storage or per-order fees, calculate the total fulfillment cost including storage, handling, shipping, returns processing, and account management. The provider with the lowest base rates rarely delivers the lowest total cost when all operational requirements are considered.
Specialized Capability Assessment
If your products require unique handling—whether temperature control, lot tracking, serial number management, or kitting services—verify that the fulfillment center has specific experience with similar requirements and established SOPs to handle them effectively.
Performance Accountability
Request specific SLA commitments for key metrics like order accuracy, same-day shipping percentage, and inventory variance rates. The best fulfillment partners offer performance guarantees with financial consequences when standards aren’t met.
Fulfillment Centers & Last Mile Delivery: How They Work Together
What happens inside the fulfillment center directly affects what happens during that crucial last mile delivery. Though warehouse operations and delivery services often operate separately, they function best when working as coordinated parts of a single process. The connection between these two phases creates opportunities to improve both customer satisfaction and operational efficiency:
Delivery Promise Accuracy
Advanced fulfillment centers calculate shipping timeframes based on real-time carrier performance data, order processing capacity, and inventory availability—ensuring that customer delivery promises are both competitive and reliable.
Carrier Selection Optimization
Rather than defaulting to a primary carrier, sophisticated fulfillment operations analyze each order against dozens of service options to identify the optimal carrier based on package characteristics, delivery requirements, and cost considerations.
Delivery Experience Enhancement
Integration between fulfillment systems and carrier networks enables value-added delivery services like appointment scheduling, delivery notifications, and package tracking—features that significantly impact customer satisfaction and reduce expensive customer service inquiries.
Returns Optimization
A well-designed fulfillment operation treats returns as a critical customer touchpoint, with streamlined processing that gets products back into available inventory quickly while providing prompt customer resolution.
Outlook: The Future of Fulfillment Centers
For forward-thinking logistics professionals, several emerging trends offer both opportunities and challenges:
Automation Integration
From autonomous mobile robots to automated storage and retrieval systems, fulfillment centers are increasingly incorporating automation to address labor challenges and throughput requirements. The most successful implementations focus on human-machine collaboration rather than complete replacement.
Distributed Fulfillment Networks
The hub-and-spoke model is evolving toward more distributed networks including micro-fulfillment centers in urban locations, enabling same-day delivery capabilities while maintaining inventory efficiency through intelligent allocation algorithms.
Sustainable Operations
Environmental considerations are becoming competitive differentiators, with leading fulfillment operations implementing eco-friendly packaging alternatives, optimized delivery routing to reduce emissions, and energy-efficient facility designs.
Staying ahead of these trends while maintaining operational excellence will separate industry leaders from followers in the coming years.
Conclusion
Fulfillment centers have transformed from simple warehouses into the backbone of successful retail operations. This shift focuses on speed, accuracy, and flexibility through better technology, smarter processes, and specialized expertise. The result is clear: businesses can meet customer expectations while keeping costs under control and adapting quickly to changes.
Whether you build your own fulfillment operation or partner with experts, what matters is the competitive edge that comes from doing fulfillment well. Companies that excel in this area succeed because customers now value delivery experience just as much as product quality and price.
Ready to transform your fulfillment strategy and turn logistics into your competitive advantage?
Discover how Anchanto’s warehouse management solution can empower your operations.
Get in Touch
FAQ
What is the difference between a fulfillment center and a distribution center?
A fulfillment center processes individual customer orders for direct-to-consumer shipments, while a distribution center primarily handles bulk shipments to retail locations or other businesses. Fulfillment centers optimize for processing numerous small orders quickly, while distribution centers focus on efficiently moving larger quantities to fewer destinations. Many operations now combine both functions in hybrid facilities with dedicated areas for each type of fulfillment.
What are the typical associated third-party fulfillment center costs?
Third-party fulfillment center pricing typically includes several components: storage fees, pick and pack fees, receiving charges, and account management fees. The total fulfillment center cost varies significantly based on order volume, storage requirements, and value-added services needed. Most providers offer volume-based discounting that reduces per-order costs as volume increases.
What types of businesses benefit most from using an order fulfillment center?
The order fulfillment center model delivers particular advantages for e-commerce businesses, subscription box companies, omnichannel retailers, businesses with seasonal demand patterns, and companies expanding into new geographic markets. The greatest ROI typically comes when order volumes reach 10-20 daily orders, when warehouse space constraints emerge, or when shipping carrier volume discounts become meaningful cost factors.
How can I track my inventory in a fulfillment center?
Modern fulfillment centers provide real-time inventory visibility through integrated management systems accessible via web portals or API connections. These systems track current stock levels, allocated inventory, pending receipts, and historical movement patterns. The best fulfillment partners offer enhanced capabilities like cycle count scheduling, lot tracking, expiration date management, and inventory forecasting tools to optimize stock levels and prevent both stockouts and overstock situations.
What should I look for when choosing a fulfillment center for my business?
When evaluating fulfillment centers, prioritize: strategic locations that minimize shipping time and cost to your customer base, technology infrastructure that integrates with your existing systems, demonstrated experience with products and order profiles similar to yours, transparent pricing without hidden fees, flexible capacity during peak periods, and carrier relationship strength evidenced by competitive shipping rates. Most importantly, verify their performance metrics including order accuracy rates, inventory variance percentages, and same-day shipping percentages to ensure they can meet your customer experience standards.