Distribution Center vs. Warehouse: What’s the Difference?
Blogs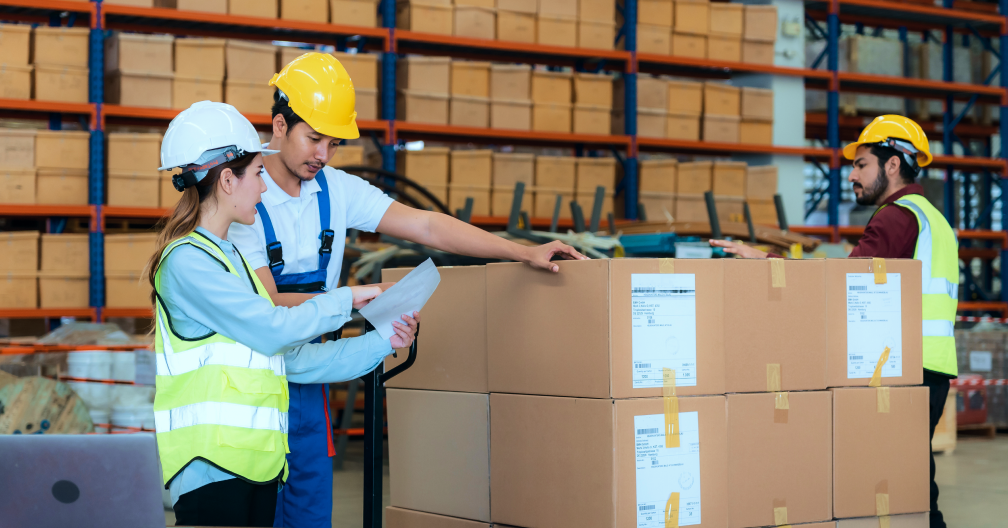
Your brand has built a reputation on exceptional customer experiences, but your last quarterly review revealed a troubling trend: delivery complaints are up 22% and cart abandonment rates are climbing. Meanwhile, competitors are advertising faster delivery times across more sales channels.
Sounds familiar? This kind of disconnect between brand promise and fulfillment reality is growing, and it’s directly impacting bottom lines. The root often lies in a fundamental question: Are you operating or employing the right type of fulfillment facility for your business needs?
Although often used interchangeably, warehouses and distribution centers represent very different operational approaches. While both handle physical inventory, their designs, functions, and optimal use cases differ significantly. Your choice between them—or how their capabilities are blended—directly impacts your costs, fulfillment speed, and ultimately, customer satisfaction. In this blog, we will examine the critical differences between warehouses and distribution centers, helping you determine which solution best aligns with your business strategy and customer expectations.
What is a Distribution Center?
Think of it as a dynamic hub where products arrive, get processed, and quickly move out to their next destination. A distribution center (DC) is a specialized facility designed primarily for the efficient movement of goods rather than long-term storage.Distribution centers serve as crucial links in the supply chain, focusing on receiving products from suppliers, processing orders, and dispatching them to customers or retail locations.
The primary function of a distribution center revolves around order fulfillment. These facilities are optimized for activities like:
- Receiving and logging incoming inventory
- Order processing and picking
- Packaging and labeling
- Sorting orders by destination
- Coordinating outbound shipping
- Managing returns and exchanges
Distribution centers typically handle a higher volume of transactions with a faster turnover rate compared to traditional warehouses. They’re often strategically located to minimize delivery times to customers or retail outlets, making them ideal for businesses prioritizing rapid fulfillment and delivery.
What is a Warehouse?
Unlike distribution centers, warehouses are primarily designed for long-term inventory storage. The traditional warehouse focuses on safely housing goods until they’re needed, with less emphasis on rapid processing or immediate distribution.
The core functions of a warehouse include:
- Long-term storage of products and materials
- Inventory management and tracking
- Preserving goods in optimal conditions
- Security and protection of valuable inventory
- Bulk storage of seasonal items or overstock
- Record keeping and inventory auditing
Warehouses offer cost-effective storage solutions, ideal for managing seasonal demand fluctuations and bulk purchasing strategies. They also provide a reliable buffer against supply chain uncertainties.. Mos tserve as stable inventory repositories rather than high-velocity processing centers.
Distribution Center vs. Warehouse: Key Differences
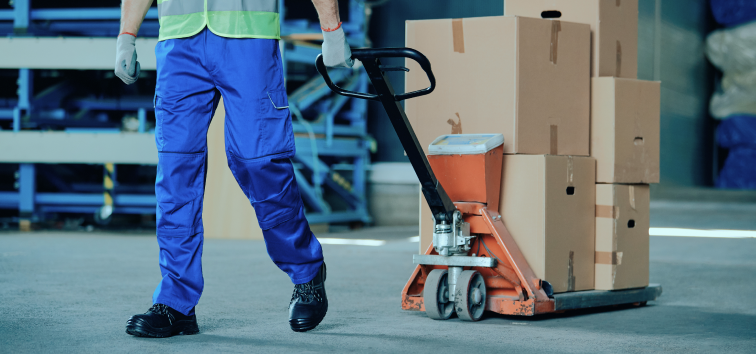
Purpose and Operations
The fundamental distinction between these facilities lies in their primary purpose. A warehouse is designed for storage, while a distribution center is engineered for movement.
Warehouses focus on securing and maintaining inventory over time. Operations revolve around inventory protection, organization, and efficient use of space. Staff primarily handle receiving shipments, documenting inventory, organizing storage, and preparing items for eventual shipment.
Distribution centers, on the other hand, are all about flow. Their operations center on quickly processing incoming goods and preparing them for immediate dispatch. Staff engage in more complex activities like order sorting, picking, packing, labeling, and coordinating with transportation networks.
Speed of Inventory Turnover
Perhaps the most telling difference between these facilities is the velocity of inventory movement:
Warehouses: Inventory typically stays for extended periods, often months or even years. The focus is on capacity and organization rather than speed.
Distribution Centers: Products rarely remain for more than a few days or weeks. The emphasis is on maintaining a steady flow rather than maximizing storage capacity.
This difference in inventory turnover directly impacts facility design, staffing requirements, technology needs, and overall operational strategy.
Technology and Automation
The different purposes of these facilities drive distinct approaches to technology and automation:
Warehouses often implement technologies focused on inventory management, space utilization, and security. This might include basic warehouse management systems (WMS), inventory tracking, and security monitoring.
Distribution centers typically invest in more sophisticated automation and technology systems to support rapid processing. These often include:
- Advanced Warehouse Management Systems
- Automated sorting systems
- Robotic picking solutions
- Conveyor systems
- Real-time tracking technologies
- Transportation management systems
- Order management integration
The technology gap between traditional warehouses and modern distribution centers continues to widen as e-commerce and consumer expectations for rapid delivery drive innovation in the distribution sector.
Integration with Shipping and Delivery
Distribution centers are designed with transportation integration as a core element. They typically feature:
- Multiple loading docks optimized for various transport types
- Cross-docking capabilities
- Sophisticated shipping preparation areas
- Close coordination with carriers and transportation networks
- Strategic geographic positioning near transportation hubs
- Last-mile delivery orchestration
While warehouses still support shipping functions, they typically involve simpler transportation requirements and handle fewer daily shipments compared to distribution centers.
Staffing and Operational Hours
The operational tempo of these facilities creates different staffing models:
Warehouses often operate during standard business hours with consistent staffing levels year-round, except during anticipated busy periods.
Distribution centers frequently operate extended hours or around the clock, with staffing levels that might fluctuate based on order volumes, seasonal demands, or promotional events. They typically require more specialized roles related to order fulfillment, shipping coordination, and returns processing.
Benefits of Using a Distribution Center
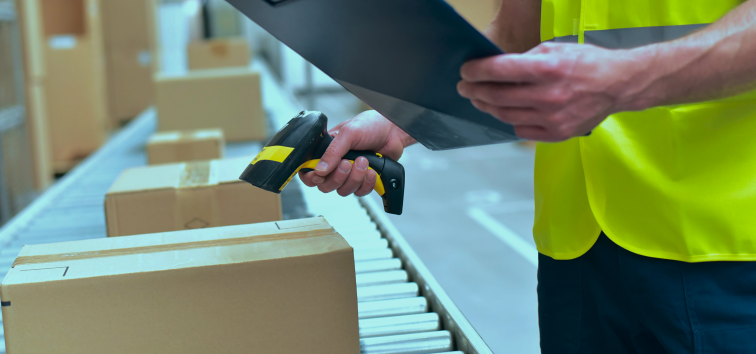
For businesses with omnichannel strategies–that prioritize rapid next-day, same-day delivery, and customer satisfaction, distribution centers offer several advantages:
Faster Order Processing: Distribution centers are optimized for speed, allowing for same-day or next-day shipping capabilities.
Reduced Transportation Costs: Strategic placement of distribution centers can significantly lower transportation expenses and delivery times.
Enhanced Customer Experience: The rapid fulfillment capabilities translate directly to customer satisfaction through faster deliveries.
Better Integration with E-commerce: Distribution centers align perfectly with online retail models that promise quick delivery.
Value-added Services: Many distribution centers offer services beyond basic storage, such as kitting, custom packaging, or product configuration.
Improved Inventory Visibility: The technology-forward approach of most distribution centers provide better real-time visibility into inventory status.
Efficiency in Returns Processing: Distribution centers typically have specialized processes for handling returns efficiently.
Benefits of Using a Warehouse
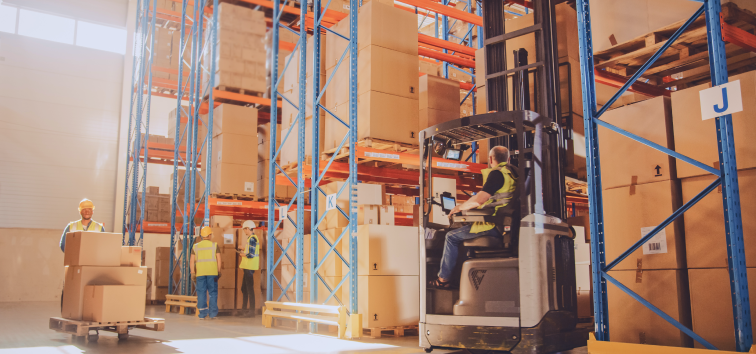
For manufacturers, wholesalers, businesses with seasonal inventory needs, and companies dealing with bulk goods or raw materials, traditional warehousing continues to offer distinct advantages for many business models:
Cost-Effective Long-Term Storage: Warehouses provide economical solutions for storing products over extended periods.
Buffer Against Supply Chain Disruptions: Larger storage capacity allows companies to maintain safety stock against unpredictable disruptions.
Bulk Purchase Advantages: Warehouses enable businesses to take advantage of volume discounts through bulk purchasing.
Seasonal Storage Capabilities: For businesses with seasonal products or demand patterns, warehouses offer space to store off-season inventory.
Simplified Operations: Warehouse operations are typically less complex than distribution centers, potentially requiring less specialized management.
Lower Technology Investment: Traditional warehousing can operate effectively with less sophisticated (and less expensive) technology systems.
Stability in Overhead Costs: Warehouses often have more predictable operational costs compared to the variable expenses of high-velocity distribution centers.
These advantages make warehouses particularly valuable for manufacturers, wholesalers, businesses with seasonal inventory needs, and companies dealing with bulk goods or raw materials.
Hybrid Setups: Best of Both Worlds
Many forward-thinking businesses are realizing that the best solution isn’t choosing between a warehouse or a distribution center, but rather combining the best of both through hybrid facilities or complementary networks. These hybrid approaches might include:
- Dedicating portions of a facility to long-term storage while optimizing other sections for rapid fulfillment
- Establishing regional distribution centers supported by centralized warehouses
- Partnering with third-party logistics (3PL) providers that offer both warehousing and distribution services
- Creating seasonal transitions where facility functions shift based on business cycles
- Implementing zone-based approaches with varying levels of automation and processing speeds
This flexible strategy allows businesses to adapt to changing market conditions, seasonal demands, and evolving customer expectations without committing exclusively to either model.
Conclusion
Choosing between a distribution center and a warehouse is more than just a matter of terminology—it’s a strategic decision that impacts how your business handles inventory and fulfills customer orders. While warehouses excel at cost-effective long-term storage, distribution centers deliver superior performance in rapid order processing and fulfillment.
For many businesses, the optimal approach involves either a hybrid model or a complementary network of both facility types. By understanding the distinct advantages of each option, you can develop a logistics strategy that balances cost considerations with customer expectations for speed and reliability.
As consumer demands continue to evolve and supply chains grow increasingly complex, the ability to strategically leverage both warehousing and distribution capabilities will remain a critical competitive advantage.
Ready to optimize your warehouse or distribution center operations?
Discover how Anchanto’s Warehouse Management System (WMS) can empower your fulfillment processes and help you meet today’s customer delivery expectations.
FAQ
What is the main difference between fulfillment vs distribution centers?
While both handle the movement of goods, fulfillment centers focus specifically on business-to-consumer (B2C) e-commerce orders, typically processing individual items for direct customer shipment. Distribution centers have a broader scope, handling both B2C and business-to-business (B2B) operations, including retail store replenishment, wholesale distribution, and e-commerce fulfillment. Fulfillment centers are essentially a specialized type of distribution center optimized for online retail.
How do I know if my business needs a distribution center vs warehouse?
If your business prioritizes rapid order fulfillment, handles high daily order volumes, requires frequent inventory turnover, or promises fast delivery to customers, a distribution center is likely more appropriate. If your focus is on long-term storage, bulk inventory management, seasonal stock holding, or you need cost-effective storage solutions with less frequent shipping, a traditional warehouse may better serve your needs. Many growing businesses benefit from a hybrid approach or gradually transitioning from pure warehousing to distribution as their fulfillment needs evolve.
What key metrics should I track differently in a distribution center vs warehouse?
For warehouses, key metrics typically include storage utilization (cost per square foot), inventory accuracy, inventory carrying costs, and storage duration. For distribution centers, focus on order fulfillment speed, order accuracy, orders processed per hour, returns processing time, shipping accuracy, and transportation costs. While both facility types should track labor efficiency and overall operational costs, the emphasis on different metrics reflects their distinct primary purposes—storage versus movement.
Can a single facility function as both a distribution center and a warehouse?
Yes, many modern facilities incorporate elements of both warehousing and distribution. These hybrid operations typically feature distinct zones—some optimized for long-term storage and others designed for rapid processing and shipping. This hybrid approach offers flexibility, allowing businesses to adjust operations based on seasonal demands or changing market conditions. The key to success is implementing management systems and processes that can effectively coordinate across these different operational modes.
How is technology used differently in a distribution center vs warehouse?
In warehouses, technology primarily focuses on inventory management, space optimization, and security systems. Distribution centers require more sophisticated technology ecosystems, including advanced warehouse management systems integrated with order management, automated sorting systems, picking automation, real-time tracking technologies, and transportation management systems. While both facility types benefit from technology, distribution centers typically require greater investment in automation and integrated systems to support their high-velocity operations and complex order processing requirements.