Unleashing the Power of WMS and Robotics for Efficient Warehouse Operations
Blogs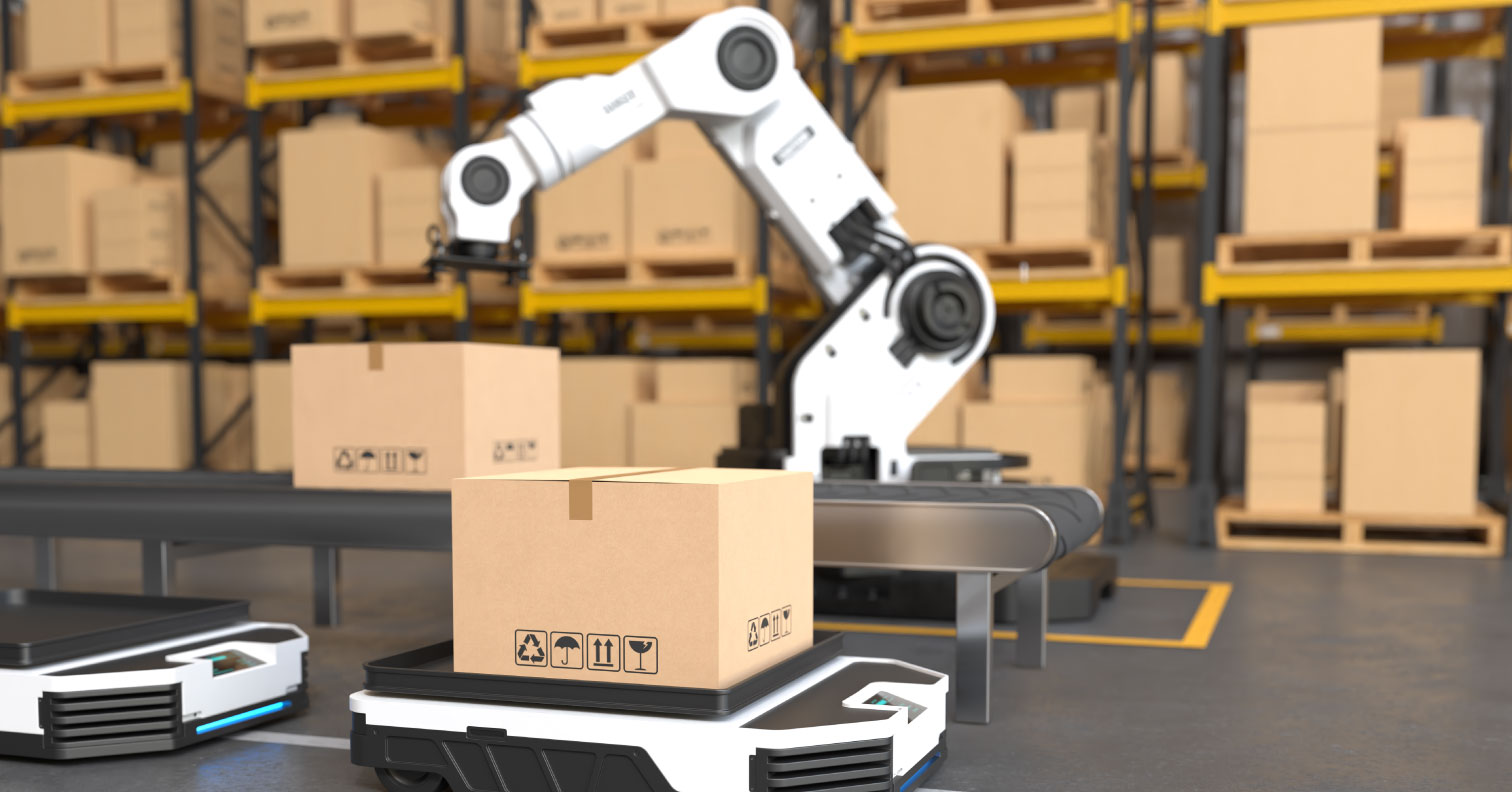
Since the e-commerce boom began, the warehousing sector has seen remarkable growth. According to a 2023 report by CBRE [1], the U.S. warehouse and distribution space expanded by 500 million square feet over the past decade, reflecting a 30% increase in capacity to meet the surging demand for online shopping. Similarly, global warehouse space is projected to grow by 8% annually through 2025.
To meet the increasing demands of brands and retail business while maintaining cost-effectiveness, warehouses are turning to technology for help. Two powerful tools that are revolutionizing warehouse operations are Warehouse Management Systems (WMS) and robotics.
When combined, a WMS and robotics create the perfect match, unleashing unparalleled power and efficiency in warehouse operations. A WMS provides advanced inventory management, order tracking, and real-time visibility, while robotics automate time-consuming tasks such as picking, sorting, and packaging.
By leveraging the WMS and robotics combination, warehouses can significantly reduce human error, improve order accuracy, and increase the speed and efficiency of order fulfillment. In this article, we will explore several intriguing aspects of implementing a WMS and robotics in warehouse operations, like:
- The Role of WMS in Warehouse Operations
- The Role of Integrating Robotics in Warehouse Operations
- Benefits of Implementing a Combination of WMS and Robotics in Warehouse Operations
- Best Practices and Training for Implementing WMS and Robotics in Warehouse Operations
- The future of WMS and robotics in warehouse operations
The Role of a WMS in Warehouse Operations
Warehouse Management Systems (WMS) have become an integral part of modern warehouse operations, providing a comprehensive solution for managing inventory, order fulfillment, and overall warehousing efficiency. A well-designed WMS acts as the backbone of a warehouse, enabling real-time visibility, data-driven decision-making, and seamless integration with other systems.
At the core of a WMS is the ability to track and manage inventory levels, ensuring that the right products are available at the right time to meet customer demands. By leveraging advanced algorithms and data analytics, a WMS optimizes storage and retrieval processes, reducing the time and resources required to fulfill orders. This improves overall productivity and enhances the accuracy of inventory records, minimizing the risk of stockouts or oversupply.
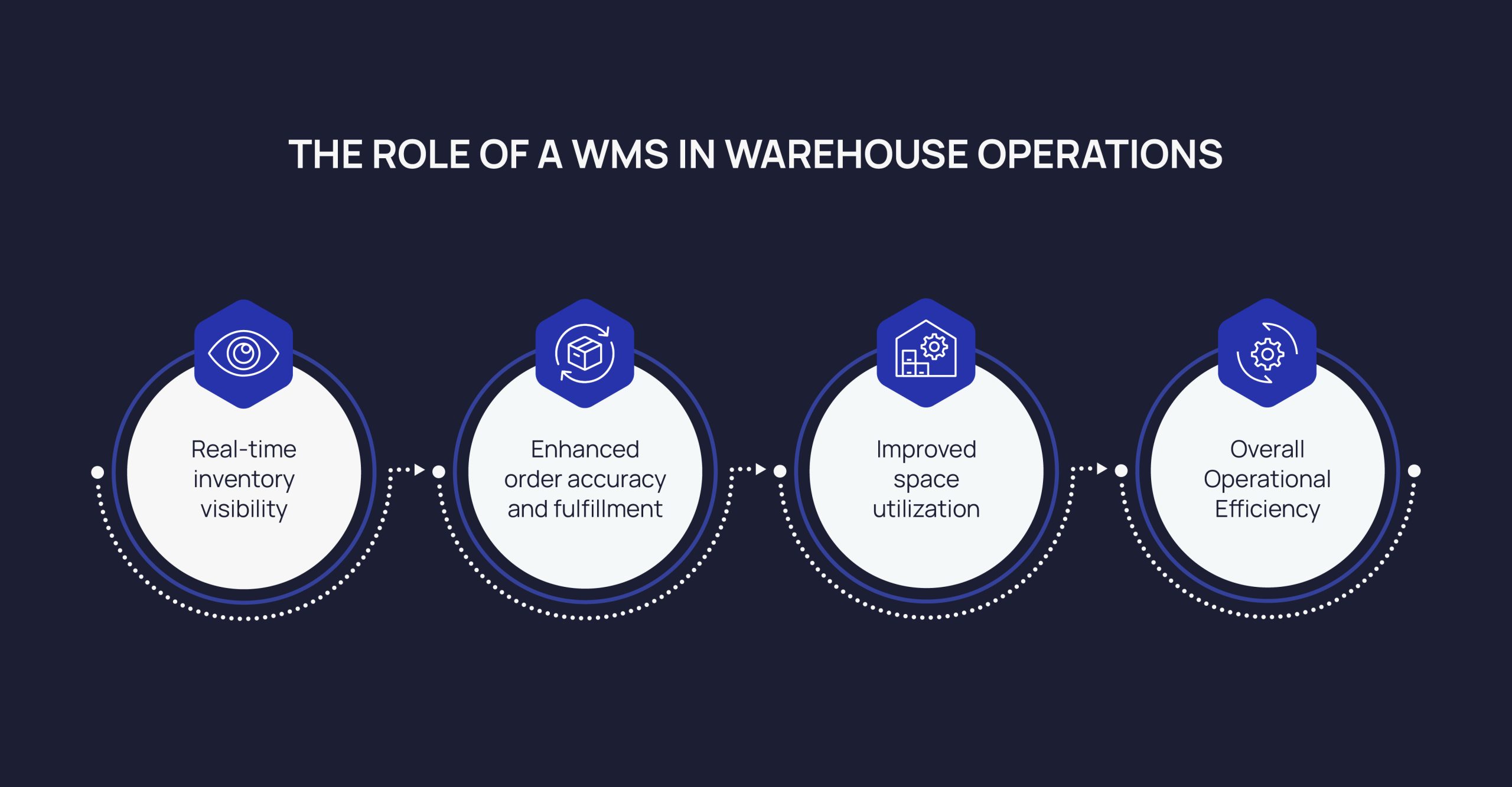
Beyond inventory management, a WMS also plays a crucial role in streamlining the order fulfillment process. By integrating with e-commerce platforms, transportation management systems, and other supply chain components, a WMS can automate the entire order-to-delivery workflow. This includes tasks such as order processing, picking, packing, and shipping, ensuring that orders are fulfilled quickly and efficiently, and meeting the ever-increasing customer expectations for fast and reliable delivery.
A robust WMS will possess features that also improve warehouse space utilization, decision making, flexibility, and much more.
The Role of Integrating Robotics in Warehouse Operations
As businesses face increasing pressure to deliver faster and more accurate fulfillment, robotics provides a transformative solution that addresses key operational challenges. From speeding up processes to improving accuracy, optimizing space, and enhancing safety, robotics offers a multitude of advantages for modern warehouses.
One of the key roles of robotics integration is increased efficiency. Robotic systems such as autonomous mobile robots (AMRs), automated guided vehicles (AGVs), and robotic arms can automate tasks like picking, packing, and sorting at much faster speeds than humans. These robots can operate around the clock without the need for breaks, ensuring continuous activity and significantly reducing processing time, which leads to a higher overall throughput.
Companies like Amazon have embraced this transformation [2], utilizing over 200,000 mobile robots in their facilities to automate tasks that were previously done manually. Their Kiva robots serve as a prime example of how robotics can simplify repetitive tasks and streamline warehouse operations.
Robotics also enhances accuracy in warehouse operations. Robots equipped with advanced sensors and machine learning algorithms can perform tasks with high precision, minimizing human errors during picking and packing. This results in more accurate order fulfillment, fewer mistakes, and reduced returns, allowing businesses to deliver consistent quality and precision in handling goods.
In addition to efficiency and accuracy, robotics optimizes space utilization within warehouses. Robots can navigate narrow aisles and high-density storage areas, allowing for better use of available space. Automated systems also enable vertical storage management and dynamic adjustment of warehouse layouts, ensuring that storage space is maximized as inventory and layout requirements change.
Another critical advantage of robotics integration is improved safety. Robots can handle hazardous tasks such as heavy lifting or dealing with dangerous materials, reducing the risk of workplace injuries. Automated systems adhere to strict safety standards and regulations, ensuring a safer working environment for employees by keeping them away from potentially harmful situations.
Cost savings is also a significant benefit of robotics in warehouse operations. Automation reduces the reliance on manual labor minimizing expenses related to training, benefits, and employee turnover. Companies like DHL, for example, have invested in robotics to automate tasks such as unloading, with plans to expand the use of robots for other functions across multiple facilities [3], leading to long-term cost savings.
Finally, robotics offers scalability and flexibility to adapt to varying business demands. Robots can be scaled up or down based on seasonal fluctuations and changing inventory levels. Moreover, they can seamlessly integrate with Warehouse Management Systems (WMS) to improve operational coordination, making them a flexible and scalable solution for modern warehouse operations.
Benefits of Implementing a Combination of WMS and Robotics in Warehouse Operations
When you choose a WMS, you reap the benefits and ease of having features and integrations that enhance your business. But the combination of a WMS and robotics can deliver powerful results in warehouse operations. These include:
a. Faster multi-seller onboarding
A WMS enables seamless onboarding by integrating with sellers’ (or brand and retailer’s) sales channels, automating workflows, and allocating storage based on inventory requirements. Robotics further accelerates this process by automating stock scanning for inventory onboarding. Together, robotics and a WMS streamline inventory storage, reduce errors, and enable faster product entry into the market.
b. E-commerce and last-mile integrations
WMS systems streamline order processing by integrating with carriers and back-office systems, improving shipment tracking and delivery coordination. When robotics is added, tasks like picking and packing are automated, speeding up fulfillment. This combination enhances order accuracy, reduces errors, and ensures faster, more reliable deliveries.
c. Real-time inventory tracking
A WMS provides real-time visibility into inventory levels on a central dashboard, ensuring better coordination and stock management. Robotics enhances this by updating stock levels as goods are picked, sorted, or dispatched. This leads to more accurate inventory control, faster fulfillment, and improved operational efficiency.
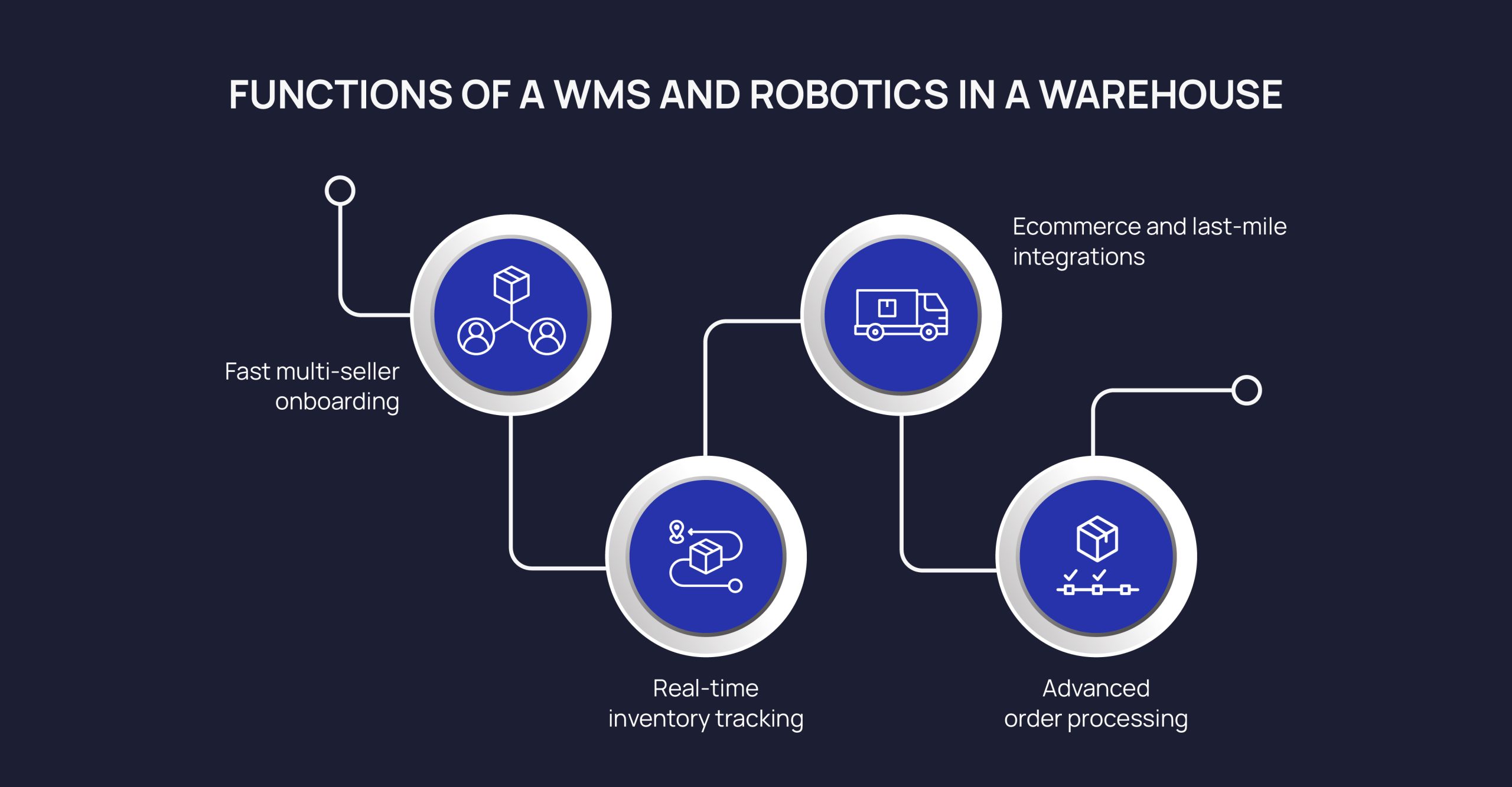
d. Advanced order processing
WMS systems enhance order processing by managing stock levels, batch and expiry dates, and storage locations. Robotics automates repetitive manual tasks and follows the WMS’s assignment of optimal routes and tasks for faster item retrieval. This integration significantly boosts productivity, reduces manual labor, and shortens order processing time.
Best Practices and Training for Implementing WMS and Robotics in Warehouse Operations
Successfully implementing a Warehouse Management System (WMS) and robotics requires a strategic and well-planned approach. Begin with a thorough assessment of your current warehouse operations, infrastructure, and pain points to identify the specific needs that these technologies should address. Once identified, develop a clear implementation plan, including a detailed timeline, resource allocation, and change management strategies to ensure a smooth transition. Prioritize compatibility with existing systems and scalability to support future growth, as well as ease of use and vendor reputation.
Equally important is the focus on training and skill development to maximize the benefits of these systems. Comprehensive training programs are essential to help employees fully leverage the capabilities of both WMS and robotics. Training should cover core functionalities, such as navigating the WMS interface, interpreting real-time data, and maintaining robotic systems for peak performance and safety. This ensures that all warehouse personnel, from managers to frontline workers, are proficient in operating these technologies.
In addition to technical skills, training programs should emphasize broader competencies like data analysis, problem-solving, and process optimization. As WMS and robotics generate large volumes of data, employees must be able to interpret this information and use it to streamline operations and drive informed decision-making. By honing these skills, warehouse staff can uncover new opportunities for efficiency and cost savings.
Finally, fostering a culture of adaptability and collaboration is critical during the integration of WMS and robotics. Change management strategies should focus on continuous learning and a mindset shift that embraces new technologies. With the right training and approach, employees will feel empowered to maximize the potential of WMS and robotics, leading to enhanced warehouse performance and long-term success.
The Future of WMS and Robotics in Warehouse Operations
In conclusion, while both WMS and robotics bring significant individual benefits to warehouse operations, their true power is unleashed when used together. By combining the data-driven precision of a WMS with the automation capabilities of robotics, businesses can achieve unparalleled levels of efficiency, accuracy, and scalability.
The synergy between these technologies enhances productivity while reducing errors and operational costs, creating a streamlined, future-ready warehouse environment. Anchanto’s WMS is designed with technology integrations in mind, offering businesses a seamless path to implementing powerful combinations and unlocking new levels of performance in their operations.
Empower Your Warehouse with a WMS that’s Future Ready!FAQs
What is warehouse robotics?
Warehouse robotics refers to the use of automated machines and robots to handle tasks within a warehouse environment, such as picking, packing, sorting, and transporting goods. These robots are designed to increase efficiency, accuracy, and speed in warehouse operations by performing repetitive or physically demanding tasks. They work alongside human staff or independently, integrating with Warehouse Management Systems (WMS) to streamline workflows and optimize inventory management. Warehouse robotics can include automated guided vehicles (AGVs), robotic arms, and collaborative robots (cobots), each contributing to a more effective and scalable warehouse operation.
What are autonomous mobile robots (AMRs)?
Autonomous Mobile Robots (AMRs) are sophisticated robots designed to navigate and perform tasks within dynamic environments, such as warehouses or manufacturing facilities, without human intervention. Equipped with advanced sensors, cameras, and artificial intelligence, AMRs can autonomously move through their surroundings, avoid obstacles, and interact with other systems or robots. They are commonly used for tasks like transporting materials, delivering goods, and managing inventory. Unlike traditional automated systems that rely on fixed paths or tracks, AMRs are highly adaptable, enabling them to efficiently optimize routes and adapt to changes in their environment.
What are automated guided vehicles (AGVs)?
Automated Guided Vehicles (AGVs) are robotic systems designed to transport materials and goods within a warehouse or industrial setting using predefined paths or tracks. Unlike Autonomous Mobile Robots (AMRs), AGVs typically follow fixed routes marked by physical guides such as magnetic strips, laser-guided systems, or overhead wires. They are used to streamline material handling processes, reduce manual labor, and improve efficiency by automating repetitive tasks such as moving pallets or bins from one location to another. AGVs can be integrated with Warehouse Management Systems (WMS) to enhance coordination and optimize logistics operations.
References –
[2] – Forbes.com – Rise Of Warehouse Robots Spurs Efficiencies—And Safety Concerns