Warehouse Racking: Types, Benefits & its Role in Inventory Management
Blogs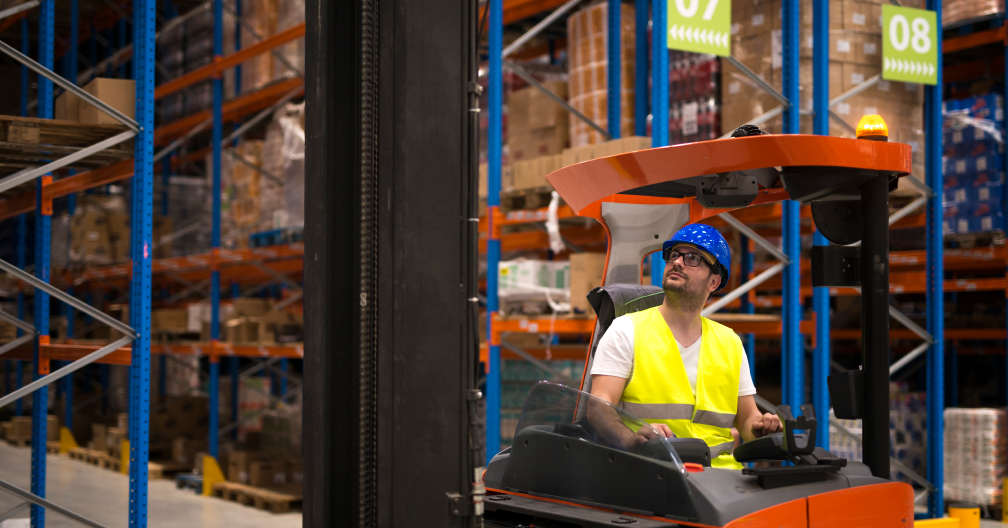
As ecommerce acceleration and omnichannel fulfillment reshape supply chain demands, warehouse optimization has become a critical competitive differentiator. The shift toward micro-fulfillment centers, dark stores, and hybrid facilities is driving innovations in racking design and implementation.
Today’s warehouse leaders are making strategic decisions that go beyond traditional storage solutions–a well-planned warehouse racking system paired with sophisticated warehouse management systems that can dramatically improve space utilization, streamline operations, and enhance overall productivity.
In this blog, we will explore the various types of racking systems, their benefits, the symbiosis with the right software systems, and how they contribute to effective inventory management.
Types of Warehouse Racking Systems
The success of your warehouse operations largely depends on choosing the right racking system. While managing warehouse operations can be challenging, understanding and overcoming common warehouse management challenges is crucial for implementing the right racking solution.
Here are the most common and effective types of warehouse racking solutions:
Selective Pallet Racking
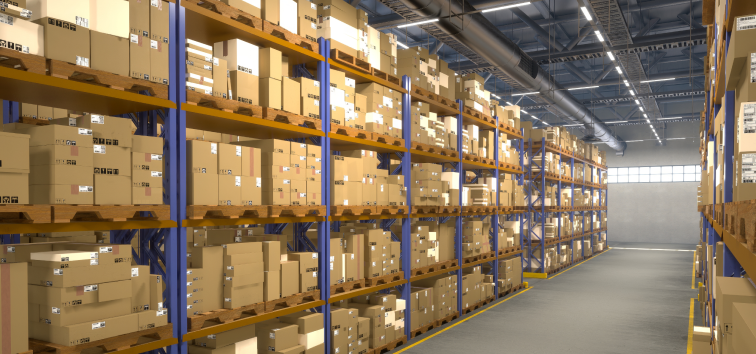
This traditional warehouse racking system remains the most widely used solution due to its versatility and cost-effectiveness. It provides direct access to all pallets, making it ideal for warehouses with diverse SKUs and frequent inventory turnover.
Drive-In/Drive-Through Racking
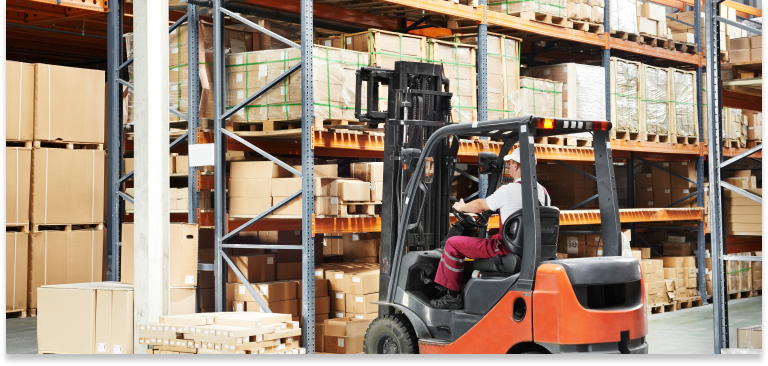
Perfect for high-density storage, these systems allow forklifts to drive directly into the racking structure. While they offer excellent space utilization, they’re best suited for businesses dealing with large quantities of similar items.
Push-Back Racking
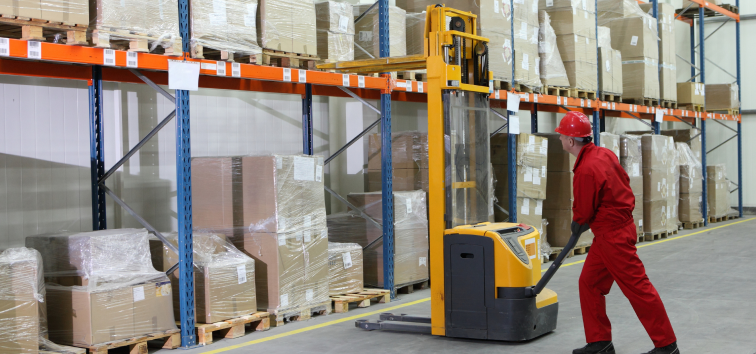
This dynamic storage system uses wheeled carts on inclined rails, allowing pallets to be “pushed back” when new ones are added. It’s an excellent choice for warehouses needing medium-density storage with good selectivity.
Automated Warehouse Racking Systems
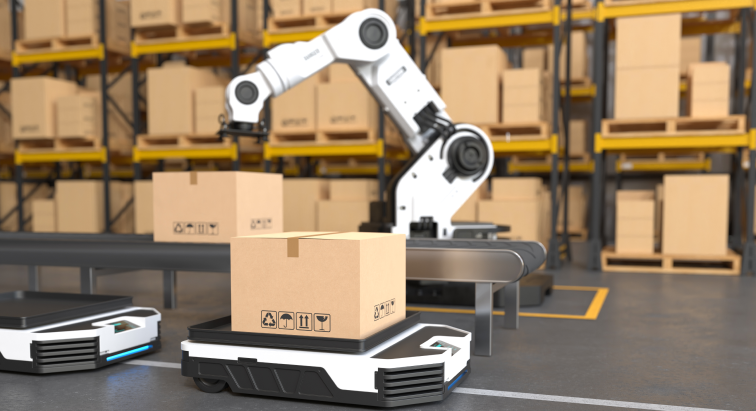
Modern warehouses are increasingly adopting automated warehouse racking systems that integrate with robotic picking solutions and warehouse management software. These systems maximize efficiency through automated storage and retrieval, reducing human error and improving throughout.
How to Choose the Right Warehouse Racking for Your Business
Selecting the right racking system hinges on four pillars: storage density , product characteristics, equipment compatibility, and budget. We break down how these factors shape your ideal solution—ensuring efficiency, safety, and adaptability for your unique needs.:
- Storage Density Requirements
Evaluate your space constraints and determine whether you need high-density storage or more accessible solutions.
- Product Characteristics
Consider the size, weight, and variety of items you store. Different products may require different racking solutions.
- Handling Equipment
Your choice of racking system should align with your material handling equipment capabilities and limitations.
- Budget Considerations
While automated warehouse racking systems offer superior efficiency, they require significant investment. Balance your immediate needs with long-term scalability.
Benefits of Implementing the Right Warehouse Racking Systems
Implementing the right warehouse racking solutions offers numerous advantages.
- Maximized Space Utilization
Proper racking systems help utilize vertical space effectively, significantly increasing storage capacity without expanding the warehouse footprint.
- Improved Organization
A well-designed warehouse racking system enables better inventory organization, making it easier to implement effective storage strategies like FIFO (First-In-First-Out).
- Enhanced Safety
Modern warehouse racking systems include safety features that protect both products and personnel, reducing workplace accidents and product damage.
- Increased Efficiency
With organized storage solutions, picking and putting away becomes more efficient, reducing operation times and improving overall productivity.
Warehouse Racking and Inventory Management
The relationship between warehouse racking and modernized inventory management is crucial for operational success. A robust inventory management system software, when paired with the right racking solution, can transform your warehouse operations. Here’s how they work together:
- Inventory Visibility
Proper racking systems paired with sophisticated inventory management software enable better inventory tracking and management, providing clear visibility of stock levels, and locations.
- Stock Rotation
Well-designed warehouse racking systems facilitate effective stock rotation, helping prevent obsolescence and ensuring proper inventory flow.
- Integration with WMS
Modern warehouse racking systems work even better when integrated with advanced warehouse management solutions (WMS), enabling real-time inventory tracking and automated operations management.
- Space Optimization
Strategic placement of racks based on inventory movement patterns helps optimize picking routes and improve warehouse efficiency.
Best Practices for Warehouse Racking Implementation
To maximize the benefits of your warehouse racking system:
- Regular Maintenance
Implement a routine inspection and maintenance schedule to ensure safety and longevity of your racking system
- Clear Labeling
Maintain clear and consistent labeling systems for easy identification and efficient picking operations.
- Staff Training
Ensure warehouse staff are properly trained on using the racking system and following safety protocols.
- Future-Proofing
Consider future growth when planning your warehouse racking layout to accommodate business expansion.
- Proper integration with Management Systems
Pick the right comprehensive warehouse management solution that can integrate with your racking system for optimized operations.
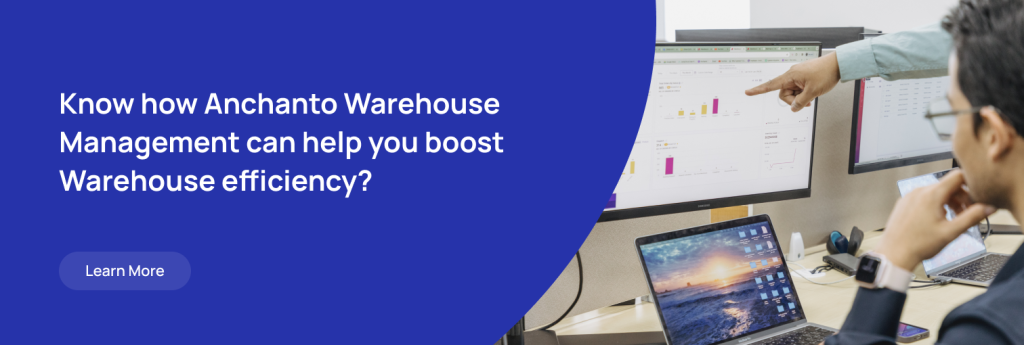
Warehouse racking systems play a vital role in modern logistics and supply chain operations. By choosing the right type of racking system—pairing it with the right software systems—and implementing it effectively, businesses can significantly improve their warehouse operations, enhance inventory management, and boost overall efficiency. Whether you opt for traditional solutions or advanced automated warehouse racking systems, the key is to align your choice with your specific business needs and future growth plans.
As warehousing continues to evolve with technological advancements, the importance of efficient racking systems only grows. Investing time and resources in planning and implementing the right warehouse racking solution will pay dividends in improved operations, reduced costs, and enhanced customer satisfaction.
Ready to optimize your warehouse operations?
Get in touch with our experts to discover the perfect racking solution for your business needs.
FAQ
What is the most cost-effective warehouse racking system for a small business?
For businesses just beginning with warehouse racking, selective pallet systems offer the most cost-effective solution. This traditional warehouse racking system provides direct access to all pallets and easy modification capabilities. It requires minimal initial investment compared to automated warehouse racking systems while maintaining excellent versatility for diverse inventory.
How do I calculate the capacity needed for my warehouse racking system?
Choosing the right warehouse racking solution depends on your space dimensions, product characteristics, and equipment requirements. Consider your current inventory levels and projected growth for 3-5 years. Professional warehouse racking system providers can help calculate precise requirements based on your operational needs and recommend appropriate solutions.
What maintenance does a warehouse racking system require?
Automated warehouse racking systems need regular visual inspections, systematic checks of connections, and quarterly structural assessments. Components requiring repair should be addressed immediately. These advanced systems require additional mechanical and electronic maintenance compared to traditional warehouse racking, along with annual professional safety audits.
What are the different types of racking systems in warehouse operations?
The main types of racking systems in warehouse environments include selective pallet racking, drive-in/drive-through racking, push-back racking, and automated systems. Each warehouse racking solution offers unique benefits depending on your storage needs, product type, and operational requirements.
What are the safety considerations when installing a new warehouse racking system?
Essential safety considerations for any warehouse racking system include building code compliance, proper floor loading capacity assessment, adequate lighting, and clearly marked weight limits. Install appropriate safety barriers, provide comprehensive staff training, and ensure regular professional inspections are conducted.