How to Optimize Labor Management with a WMS?
Blogs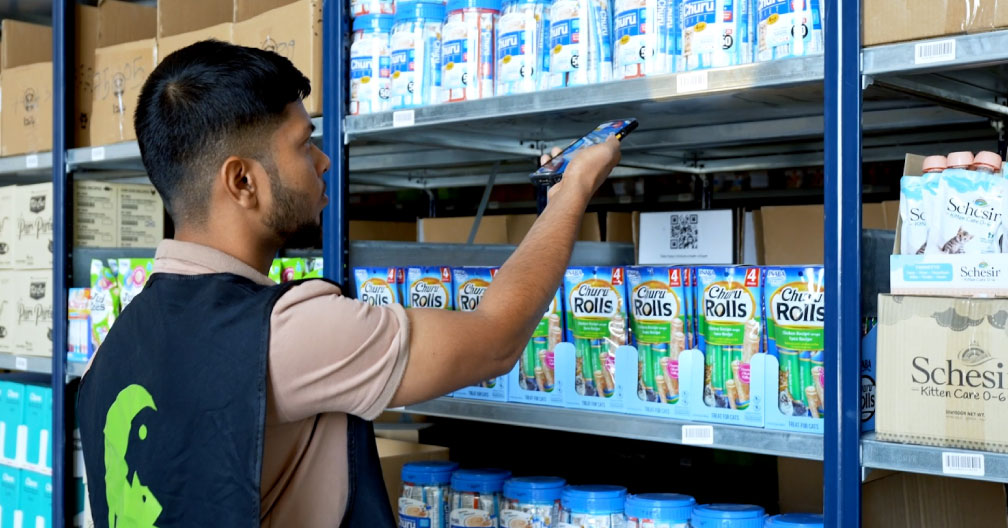
While Logistics businesses today have the option of running their warehouses with software and robotics, they still depend on physical labor. According to research published in the Harvard Business Review [1], warehouse and logistics automation works better with human partners. The research further states that human-robot collaborative systems (or cobots), which have been adopted by companies such as DHL and CEVA, saw benefits including reduced travel times and fatigue levels, higher productivity, and more motivated employees.
Although this is great news for those working at warehouse companies, it still leaves logistics and warehouse businesses open to the challenge of unoptimized labor management. For improved productivity, reduced costs, less idle time, and zero overstaffing, optimized labor management is vital. For this, it’s essential to mindfully incorporate automation with the right technology like a Warehouse Management System.
Through this guide we will equip you with the knowledge and tools to achieve labor management optimization success. In the coming sections, you’ll learn a great deal about the:
- How to Optimize Labor Management with a WMS
- Steps to Implement Labor Management Optimization with a WMS
- Choosing the Right WMS for Labor Management Optimization
- Best Practices for Labor Management Optimization with a WMS
- Conclusion: Unlocking Efficiency and Productivity with Labor Management Optimization and WMS
How to Optimize Labor Management with a WMS
Labor management optimization in a warehouse refers to the process of improving workforce efficiency by aligning tasks, shifts, and workloads with employee skill sets and availability. When using a WMS for labor management optimization, you can track productivity, assign tasks based on real-time needs, and ensure optimal resource allocation, leading to increased productivity and reduced operational costs.
Here are a few points that dive into the detailed outcomes of labor management with a WMS:
- Workforce productivity: Implementing labor management optimization with a Warehouse Management System (WMS) can provide numerous benefits for your business. One of the primary advantages is improved workforce productivity. When a WMS automates and streamlines various warehouse tasks, such as order picking, packing, and inventory management, it allows your employees to focus on more value-added activities, like quality control, customer service and support, decision making, and process optimization. By reducing the time spent on manual and repetitive tasks, workers can dedicate their efforts to higher-priority responsibilities, leading to increased efficiency and output.
- Workforce productivity: Implementing labor management optimization with a Warehouse Management System (WMS) can provide numerous benefits for your business. One of the primary advantages is improved workforce productivity. When a WMS automates and streamlines various warehouse tasks, such as order picking, packing, and inventory management, it allows your employees to focus on more value-added activities, like quality control, customer service and support, decision making, and process optimization. By reducing the time spent on manual and repetitive tasks, workers can dedicate their efforts to higher-priority responsibilities, leading to increased efficiency and output.
- Streamlined workforce planning, scheduling, and cost: Implementing labor management optimization with a WMS also enables your warehouse to streamline workforce planning, scheduling, and costs. For instance, the labor management capabilities of an advanced WMS provide insights into your workforce’s productivity, task completion times, and resource utilization. This data can be used to create more accurate labor forecasts, optimize shift schedules, and ensure the right number of employees are deployed to handle the workloads. This leads to reduced labor costs and improved customer service.
- Real-time labor tracking and performance monitoring: A WMS with labor management capabilities provides live updates on employee activities, task completion times, and productivity metrics. This data can be used to identify bottlenecks, recognize high-performing employees, and implement targeted training or coaching programs to enhance overall workforce performance.
- Workflow optimization: Automated task assignment and workflow optimization is also an essential benefit of labor management optimization with a WMS. By leveraging the system’s intelligence, warehouse managers can streamline the assignment of tasks to employees based on factors such as skill sets, availability, and proximity to work zones. This helps to minimize travel time, reduce idle time, and ensure a balanced workload distribution, leading to increased productivity and reduced labor costs.
Steps to Implement Labor Management Optimization with a WMS
There are three key steps to effective warehouse labor management optimization when using a WMS. These include:
- A thorough assessment of your current workforce management practices and identify areas for improvement. This step requires you to analyze your existing labor planning processes, identify bottlenecks or inefficiencies, and determine the specific labor management challenges you aim to address with a WMS.
- Leveraging a WMS that offers robust labor management capabilities. Once you know what areas of your workforce you need improve, look for a system that provides features such as workforce planning and scheduling, real-time labor tracking, performance analytics, and automated task assignment. Ensure that the WMS aligns with your business requirements and can seamlessly integrate with your existing warehouse operations and other enterprise systems.
- Configuring the labor management settings and workflows within the system. This may involve defining employee profiles, setting up work zones, configuring task prioritization rules, and customizing performance metrics and reporting. It’s crucial to involve your warehouse team in this process to ensure the labor management optimization aligns with their day-to-day operations and preferences.
Choosing the Right WMS for Labor Management Optimization
When selecting a WMS for labor management optimization, it’s essential to consider the specific features and capabilities that align with your business requirements. So ensure you look out for Warehouse Management Software that provide:
- Workforce planning and scheduling: As discussed, this will allow you to create efficient shift patterns, assign tasks based on employee skills and capacity, and forecast labor needs, especially during peak seasons, based on historical data and projected demand.
- Real-time labor tracking and performance monitoring: The system should provide detailed insights into employee productivity, task completion times, and resource utilization, enabling you to identify areas for improvement and make data-driven decisions to enhance overall workforce efficiency.
- Automated task assignment and workflow optimization: These are also key features to look for in a WMS that you plan to use for labor management optimization. The system should be able to analyze the warehouse layout, employee skills, and work priorities to automatically assign tasks and optimize workflows, reducing manual effort and ensuring a balanced workload distribution.
Best Practices for Labor Management Optimization with a WMS
Once you implement a WMS to manage your inventory and optimize labor, it’s essential to regularly review the outcomes. For example, you can check and adjust your workforce planning and scheduling based on insights from the Warehouse Management System. As your business and operational requirements evolve, it’s essential to revisit your labor forecasts, shift patterns, and task assignments to ensure they remain aligned with the changing demands. Leverage the real-time data and analytics provided by the WMS to make informed decisions and continually optimize your workforce deployment.
You can also ensure employees are well-versed in using the WMS, especially after updates or changes in workflows. Regular training sessions help them understand how to make the most of automation and analytics features, increasing productivity. You can even leverage the WMS data to identify top performers and create incentive programs based on measurable outputs like task completion times or accuracy rates. This can motivate employees and encourage better performance across the board.
Conclusion: Unlocking Efficiency and Productivity with a WMS
It’s quite clear that labor management optimization with a Warehouse Management System helps unlock significant improvements in workforce productivity and operational efficiency. Optimized labor management is the need of the hour as labor costs continue to keep inflation elevated [2]. By automating task allocation and providing real-time tracking of employee performance, a WMS ensures that labor resources are utilized effectively, reducing inefficiencies and minimizing errors caused by manual processes. This optimization also allows businesses to swiftly adapt to demand fluctuations, keeping labor costs under control. With detailed insights into workforce activities, managers can make data-driven decisions that enhance employee engagement and productivity.
Moreover, a WMS facilitates improved training and performance management by identifying skill gaps and recognizing top performers. This empowers managers to implement targeted training programs and optimize shift schedules based on real-time data, ensuring the right personnel are in the right positions at the right times. Ultimately, by leveraging a WMS for labor management, organizations can foster a more efficient and motivated workforce, driving overall operational success in a competitive landscape.
Get Firsthand Experience Labor Management with WMSFAQs
What is the role of automated task assignment in labor management?
Automated task assignment uses tech and data to automatically assign tasks based on worker skills, availability, and task priority levels. This ensures that the right employees are doing the right jobs at the right time, reducing idle time and enhancing productivity. The automation minimizes manual errors and speeds up decision-making, further streamlining warehouse operations.
What challenges can businesses face when implementing labor management optimization?
When implementing labor management optimization with a WMS, businesses may face challenges such as employee resistance to new technology, the need for proper training, and the integration of the WMS with other existing systems. Additionally, the accuracy of data input is critical for successful optimization, and poor data quality can lead to inefficient task assignments and suboptimal labor performance.
References –
[1] – hbr.org – Research: Warehouse and Logistics Automation Works Better with Human Partners
[2] – Spglobal.com – Labour costs keep inflation elevated worldwide in June